Dự án Horizon 2020 của Liên minh Châu Âu có tên là SMall Innovative Launcher for Europe” (còn được gọi là Dự án SMILE) nhằm mục đích thiết kế các bộ phận phóng vệ tinh nhỏ (khoảng 150 kg) vào quỹ đạo mặt trời (500 km). Viện Cấu trúc và Thiết kế của Trung tâm Hàng không Vũ trụ Đức (Deutsches Zentrum für Luft- und Raumfahrt , có trụ sở tại Stuttgart, Đức, là một trong 14 tổ chức tham gia và chịu trách nhiệm phát triển; tập trung vào cải tạo và tái sử dụng hệ thống, đưa ra giải pháp tiết kiệm chi phí tối ưu.
Markus Kuhn và Ilja Müller, Giám đốc dự án Injector Head, DLR nói: “Công nghệ in 3D Kim loại của 3D Systems kết hợp với các giải pháp thiết kế thông minh đã giúp chúng tôi có thể hiện thực được rất nhiều ý tưởng trong thời gian ngắn.” |
CÁC THÁCH THỨC
Do cấu tạo phức tạp của thành phần đầu kim phun của động cơ ôxy lỏng, DLR đã hợp tác với Trung tâm Khách hàng (CIC) của Hệ thống 3D Systems ở Leuven (Bỉ) để đưa ra các giải pháp thiết kế và in 3D Kim loại nhằm đáp ứng các yêu cầu của DLR.
Leuven CIC của 3D Systems là một trong bốn trung tâm trên toàn Thế giới chuyên thúc đẩy các ứng dụng tiên tiến bằng cách cung cấp cho khách hàng quyền truy cập vào các tài nguyên cần thiết để phát triển, xác nhận và thương mại hóa sản phẩm của họ.
GIẢI PHÁP
Bằng cách chọn phương pháp in 3D Kim loại (DMP) đầu kim phun đồng trục, DLR đã tìm cách tận dụng một số lợi ích chính của việc công nghệ in 3D, bao gồm:
Giảm số lượng bộ phận với thiết kế nguyên khối cũng như Tích hợp các tính năng chính như kênh làm mát để có hiệu suất tốt hơn cho hệ thống đẩy tổng thể.
Markus Kuhn và Ilja Müller quản lý dự án đầu kim phun tại DLR cho biết họ đã nghiên cứu rất kỹ danh sách các hãng công nghệ in kim loại trên Thế giới và quyết định lựa chọn hãng 3D Systems (Mỹ) làm đối tác dựa trên những thành công của hãng trong việc cung cấp các giải pháp in 3D kim loại cho các ứng dụng hàng không vũ trụ
“Dựa trên sự thành công của các sáng kiến dành cho không gian vũ trụ. Chúng tôi thấy công nghệ in 3D của hãng 3D Systems (Mỹ) hoàn toàn phù hợp để cung cấp các giải pháp cho sản xuất của đầu kim phun, đem lại các khả năng mới về tích hợp cảm biến và phân phối nhiên liệu cũng như chất làm mát,” Kuhn nói.

01. Tối ưu hóa thiết kế kim phun nhiên liệu và giảm số lượng các bộ phận
Kim phun của tên lửa là bộ phận để đẩy nhiên liệu và chất oxy hóa đi vào buồng đốt. Hệ thống này nếu được tối ưu sẽ nâng cao hiệu suất và kiểm soát tốt được quá trình đốt cháy cần thiết để di chuyển tên lửa.
PHÂN TÍCH GIẢI PHÁP THAY THẾ SẢN XUẤT TRUYỀN THỐNG BẰNG GIẢI PHÁP IN 3D KIM LOẠI ĐỐI VỚI HỆ THỐNG ĐẦU KIM PHUN ĐỘNG CƠ TÊN LỬA:
Tối ưu hóa hiệu suất của sản phẩm thông qua các thiết kế mới để phân phối nhiên liệu và chất làm mát;Dễ dàng thực hiện các kênh cảm biến nhiệt độ và áp suất 3D;
Loại bỏ các bước sản xuất và lắp ráp trung gian;Tối ưu hóa độc lập hiệu suất nhiệt, khối lượng và thủy lực mà không bị hạn chế bởi các phương pháp chế tạo truyền thống;
Tránh các điểm lỗi lắp ráp và nâng cao chất lượng với thiết kế nguyên khối;
Giảm các bước gia công để tạo ra một kim phun tích hợp cao và đa chức năng.
Bằng cách sử dụng in 3D kim loại, DLR đã có thể thay đổi mạnh mẽ phương pháp thiết kế của kim phun đồng trục và giảm tối đa số lượng các bộ phận, góp phần giảm đáng kể thời gian và chi phí sản xuất.
Việc giảm số lượng từ 30 bộ phận xuống còn 01 bộ phận đã góp phần giảm 10% trọng lượng. Việc loại bỏ các bộ phận thường xuyên hư hỏng đồng nghĩa với việc giảm bớt các biện pháp kiểm soát chất lượng. Từ đó giúp cải thiện hiệu suất của toàn hệ thống.


Theo Koen Huybrechts – (Kỹ sư dự án): “Công nghệ in 3D kim loại là giải pháp duy nhất đáp ứng yêu cầu về hiệu suất và làm mát được tối ưu hóa. Đơn giản hóa sự phức tạp trong thiết kế của các kênh cảm biến, áp suất và nhiệt độ , lắp ráp và sản xuất với các quy trình nhất quán”.
02. Quy trình in 3D Kim loại bộ phận Đầu kim phun cho động cơ tên lửa
Phần mềm: 3DXpert ™ (3DXpert là một phần “mềm tất cả trong một”)Máy in 3D Kim loại (DMP): ProX DMP 320
Vật liệu in: LaserForm ® Ni718 (A) một hợp kim Inconel chống oxy hóa và ăn mòn.
LaserForm Ni718 (A) có độ bền kéo, mỏi, rão và đứt gãy ở nhiệt độ lên đến 700°C, và do đó lý tưởng cho các ứng dụng nhiệt độ cao.
Processing sau in: Được xử lý bằng nhiệt để loại bỏ hoàn toàn support với thiết bị phóng điện (EDM).


03. Thay thế hoàn toàn phương pháp sản xuất truyền thống. Tăng tốc chu kỳ thiết kế
Với các lựa chọn vật liệu Kim loại có sẵn của 3D Systems, DLR đã tăng tốc trong việc thử nghiệm các thiết kế bỏ qua phương pháp làm khuôn truyền thống.
Khả năng này rất quan trọng đối với chu trình thiết kế của DLR, vì nó phải đối mặt với vấn đề “Thời gian”. Vì vậy, chỉ sau vài tuần họ đã dẫn đầu cho thiết kế giai đoạn một và tiến vào giai đoạn thử nghiệm một cách thần tốc.
Kuhn và Müller cho biết: “Sự kết hợp của ProX DMP 320 và kiến thức 3D Systems về thiết kế cho in 3D Kim loại đã giúp chúng tôi có thể thử nghiệm nhiều tùy chọn thiết kế hơn trong thời gian ngắn hơn nhiều”, Kuhn và Müller nói.
In 3D kim loại cho phép DLR áp dụng kỹ thuật phun đồng trục với phần tử kim phun xoáy kép để tối ưu hóa sự hòa trộn chất oxy hóa – nhiên liệu của đầu kim phun.
Hai giải pháp làm mát khác nhau đã được thực hiện, mỗi giải pháp sử dụng các kênh nhỏ với kích thước tính năng tối thiểu là 0,2 mm và tỷ lệ chiều dài / đường kính tối đa là 45.
Thiết kế cũng tích hợp tính năng tạo màng trong đầu kim phun, cho phép các kỹ sư điều chỉnh tốc độ dòng chảy của màng trực tiếp tại kim phun.



KẾT QUẢ NÂNG CAO HIỆU SUẤT VÀ TĂNG HIỆU QUẢ SẢN XUẤT Các tính năng của bộ phận được tối ưu hóa: Giảm 10% trọng lượng Giảm 29/30 chi tiết lắp ráp: Tăng tốc chu kỳ thiết kế và giảm tối đa chi phí sản xuất THÀNH CÔNG CỦA CÁC DỰ ÁN KHÁC TRONG LĨNH VỰC HKVT NHỜ SỬ DỤNG PHƯƠNG PHÁP IN 3D KIM LOẠI (DMP) CỦA HÃNG 3D SYSTEMS Giải pháp In 3D vât liệu Kim loại (DMP) đã tạo nên những thay đối quan trọng trong lĩnh vực Hàng không và Vũ trụ bởi những lợi ích to lớn mang lại, bao gồm: Giảm trọng lượng. Tiết kiệm nhiên liệu. Hiệu quả hoạt động cao hơn, hợp nhất các bộ phận, tăng thời gian đưa ra thị trường và giảm các chi phí bảo trì đối với các bộ phận. Các dự án gần đây đã chứng minh tính hiệu quả của công nghệ in 3D Kim loại (DMP) của 3D Systems trong lĩnh vực hàng không vũ trụ bao gồm: Bộ lọc tần số vô tuyến (RF) in 3D đầu tiên đã được thử nghiệm và xác nhận để sử dụng trong các vệ tinh viễn thông thương mại. Bộ lọc mới của Airbus Defense and Space giảm trọng lượng 50% so với các thiết kế trước đây. Chân đế bằng titan nhẹ hơn 25% và có tỷ lệ độ cứng trên trọng lượng tốt hơn so với các chân đế được sản xuất theo phương pháp truyền thống, được giới thiệu thông qua sự hợp tác giữa Thales Alenia Space và 3D Systems. Các bộ phận động cơ do Cơ quan Vũ trụ Châu Âu (ESA) và Hệ thống 3D tạo ra trong một dự án giúp tiết kiệm trọng lượng, đơn giản hóa việc lắp ráp, sản xuất tốc độ và cho phép thích ứng thiết kế giai đoạn cuối dễ dàng hơn. Khung máy bay topology với tối ưu hóa làm giảm trọng lượng bằng 70% trong khi thỏa mãn tất cả các yêu cầu chức năng và đáp ứng các thách thức của GE Aircraft. Các yêu cầu này được thực hiện bởi dự án “SMall Innovative Launcher for Europe” được điều phối bởi NLR, đã nhận được tài trợ từ ‘Chương trình nghiên cứu và đổi mới Horizon 2020’ của Liên minh Châu Âu theo thỏa thuận tài trợ số 687242. |
TIN TỨC KHÁC
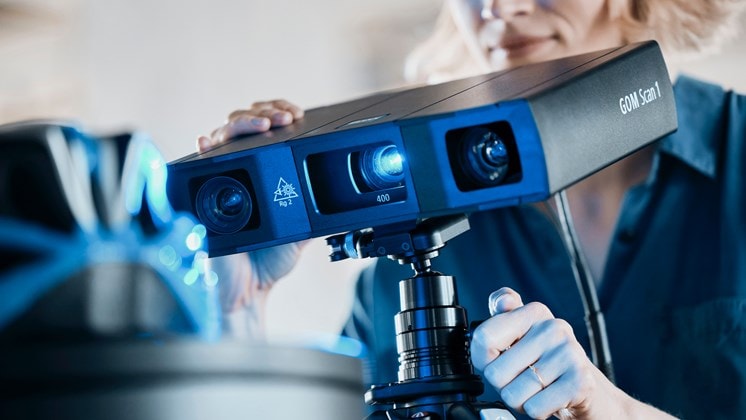